Humidity Protection
The porous epoxy coating of radial dipped film capacitors cannot be expected to provide reliable humidity protection where moderate to severe humidity conditions exist, even when potting compound such as bitumen is used. In addition, since there is no clearly defined seating plane, components rest on the “lacquered pants' that can and do develop fissures at the pin exit points when parts are automatically inserted, thus further compromising their ability to resist the effects of humidity.
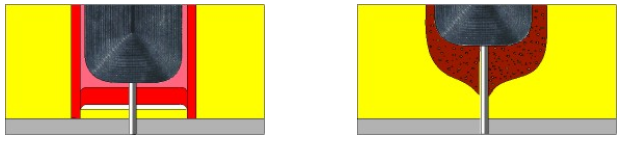
|
Box Type | Dipped Type |
- Two casting steps guarantee high humidity protection. - Homogenous encapsulation without air enclosures. - Case and pin exit points secure from high humidity. - Additional protection by cast sealing is not necessary. | - Very porous coating with visible air enclosures. - Mechanical stress during insertion leads to cracks around the pin exit points. - Insufficient humidity protection due to thin and irregular encapsulation. - Bitumen or tar casting does not provide the expected protection. |
Uniform Dimensions
Radial box film capacitor provides uniform dimensions for purposes of optimizing space and second sourcing. Further, it allows for greater flexibility in automatic insertion including robotic insertion of larger parts.
Box Type
- All dimensions clearly defined. - Allows for close placements of parts. - Easy second source because of the standardized box size.
| 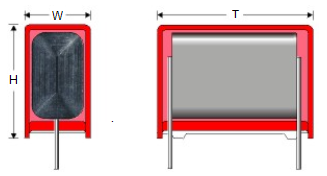
|
Dipped Type
- Only pin spacing is defined. - All other dimensions are undefined. - No standardized body size (second source) - Additional space is required between components due to changes in pin outlets and dimensions. | 
|
Exact Setting on PC-Board
Since radial dipped film capacitors rest on their pins rather than on the case or 'standoff-feet', any vibration that the capacitor element may be experiencing will be transmitted through the pins to the solder joints. This is of particular concern in AC applications where self-generated electro-mechanical vibrations accelerate the ageing of the solder joints.
Box Type
- Capacitors rest on 'standoff-feet'. - No stress on pins. - Electro-Mechanical vibrations do not impact solder joints. - Exact setting on PC-Board. - Small footprint on PC-Board.
| 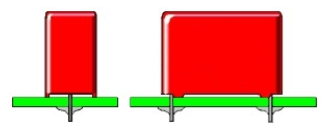
|
Dipped Type
- Capacitors rest on 'Solder joints'. - Electro-Mechanical vibrations can lead to accebrated ageing of solder joints. - More space required to avoid short circuits.
|  |
Flammability Resistance
The extremely thin covering, plus the presence of air pockets contained within the coating, makes the dipped film packaging of doubtful value with regard to passive and active flammability. This is especially the case when the applications does not use any potting compound. On the other hand, the mechanical integrity of the box and cast resin technology provides a high level of flammability resistance when the capacitor is used in AC applications such as in a power line filter or in series with the lamp.
Basically all plastic film dielectrics are flammable. Only encapsulation protects the capacitor against fire.
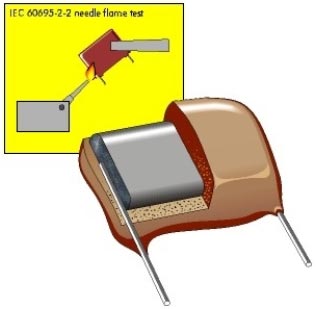 | Box type
- Uniform thickness of encapsulation. - High flammability protection in accordance with UL 94 V-0 - No cast sealing necessory
|
Dipped Type
- Epoxy material may or not be passively flammable. - Thin coating gives quick access to winding element after short application of flame. - Air bubbles in coating stimulate the flames. - Higher fire risk when tar is used. |
When radial box film capacitors are used, the need for potting disappears, since the box capacitor provides sufficient humidity and flammability protection, as well as mechanical integrity, in the face of externally or internally generated shock and vibration.
The need for qualified capacitor applications to operate for many years without the maintenance or replacement in often times difficult environmental and operating conditions, makes it critical that the components meet the highest standards of packaging technology.
Without such standards, safe and reliable operation over the life of the product cannot be guaranteed. The box film technology is designed to meet this challenge both in radial and SMD version.